Sometimes, it’s the things we might not immediately think of as risks to business that affect your clients’ bottom line the most. Here, we look at some of the more obscure factors that could affect their revenues and learn how a proactive approach to building and maintaining supply chains can help your clients become more resilient.
At a Glance
- Your clients’ supply chains may be more vulnerable to disruption than they think.
- Anything from unhappy staff to evolving cyber threats could impact the flow of essential items to their business.
- Brokers can help their clients build more resilient supply chains by diversifying and localising suppliers and investing in team morale.
Political unrest
More than a third (37% [S1] ) of UK businesses have been affected by recent disruption to shipping routes in the Red Sea. Manufacturers, retailers and wholesalers are among the most likely to be affected and some firms have seen shipping costs rise by 300%. Tensions in the region have been a logistical nightmare for SMEs, adding weeks to delivery times and highlighting vulnerabilities in supply chains.
The savviest of business leaders are planning for the future by turning to regional suppliers. The trend is particularly popular with consumer product companies, with 71% [S2] of the businesses investing in localising their supply chain. For a truly robust approach, your clients might want to consider building a contingency plan. Our Business Continuity Services can help you identify geopolitical risks and improve your clients’ chances of consistently providing their products and services to customers.
Internal teams
Ask most CEOs where they think their next supply chain issue might come from and many of them won’t answer with ‘unhappy staff’. Most of us look outwards to identify risks but unmotivated or disgruntled employees could be one of the most overlooked threats to supply chains. No one has greater access to the flow of goods at a company and unengaged team members are more likely to make mistakes when managing inventory, or even deliberately sabotage operations.
Getting employees ‘on side’ is one of the best ways to avoid this kind of supply chain disruption. You might want to talk to your clients about the importance of building a strong workplace culture. Investing in staff through regular training and skill development programmes could help to boost morale and encourage employee satisfaction and loyalty.
Unengaged team members are more likely to make mistakes when managing inventory, or even deliberately sabotage operations.
Freight bottlenecks
Many, if not all, of your clients will be familiar with the Suez Canal obstruction in 2021. Their supply chains may have been affected too, as the route carried 12% [S3] of global trade at the time. The grounded ship held up an estimated £7bn [S4] of goods each day for 6 days and the chances of something similar happening again are surprisingly high. Whether it’s a grounded ship, extreme weather conditions or political tensions, the narrow routes are vulnerable to a wide range of disruptions and they’re surprisingly widespread. Freight bottlenecks can be found between in Central America at the Panama Canal and between Europe and Africa at the Strait of Gibraltar, and the list doesn’t end there.
As a broker, you can help build resilience to shipping delays by encouraging your clients to maintain flexible supply agreements with multiple carriers. By reducing dependencies on limited transit routes, businesses improve their chances of running as usual. Freight forwarding platforms can also help SMEs track key routes, analyse the data and plan for any cargo complications.
Resurgence of Covid-19
Lockdowns may have come and gone but the chances of new variants emerging remains. We only have to look as far as late 2023 and the outbreak of JN1, to learn that we’re not quite over the covid hill. That’s why preparing for new containment measures is always a good idea. To mitigate the risks to their businesses, your clients should maintain an agile supply chain that can quickly adjust to changes in health regulations and travel restrictions. A diverse network of suppliers, stockpiles of essential inventory and scenario planning can also help mitigate any future pandemic-induced risks.
New and evolving cyber threats
The digitisation of supply chains is helping business owners to make better-informed decisions around demand forecasting, inventory management and much more. Unfortunately, technology exposes supply chains to a unique set of risks too. Malware, phishing and other malicious online attacks can wreak havoc with your clients’ businesses. Whether it’s disruption to receiving goods, or financial losses, cyber-attacks have serious consequences for SMEs.
Robust cybersecurity, vulnerability assessments and employee training on cyber hygiene should be part of all businesses’ plans to reduce their online risk. Perhaps it’s time you talked to your clients about finding a trusted IT partner. An experienced specialist could provide risk management guidance, help plan a response to a security incident and offer support should a business fall foul of an attack.
Scope 3 scrutiny
There’s never been more pressure on your clients to run their businesses sustainably. Scope 3 emissions, or greenhouse gases produced across a company’s entire supply chain, account for 80-95% [S5] of their total carbon footprint. By disclosing these emissions and showing a willingness to cut them down, your clients could attract potential investors and growth opportunities.
The issue for many businesses is understanding emissions across multiple tiers of suppliers, diverse activities and a range of locations. Finding suppliers who meet the highest environmental standards could lead to disruptions in receiving stock and inventory. The most forward-thinking business leaders are building relationships with their suppliers to collectively work on reducing emissions. A community-based, or shared approach to the problem demands time and effort but could secure a better future for your clients’ bottom line and the planet.
Port congestion and warehouse shortage
Many of the factors listed above are already impacting supply chains. Whether it’s blocked shipping routes, increased shipping costs or surges in post-pandemic demand, issues have piled up over time and led to congestion at major ports. The delays to businesses can affect the delivery of products and services, and your clients’ revenues. Brokers who add the most value to their clients are encouraging business owners to increase inventory levels. By stocking higher volumes of essential items, businesses are less exposed to the risks congestion brings. Using technology to manage inventory and building a network of diverse and local suppliers, can also help to make supply chains more resilient.
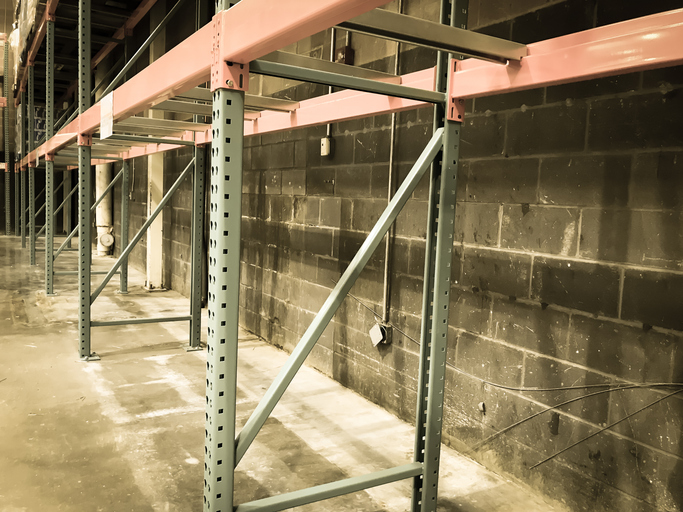
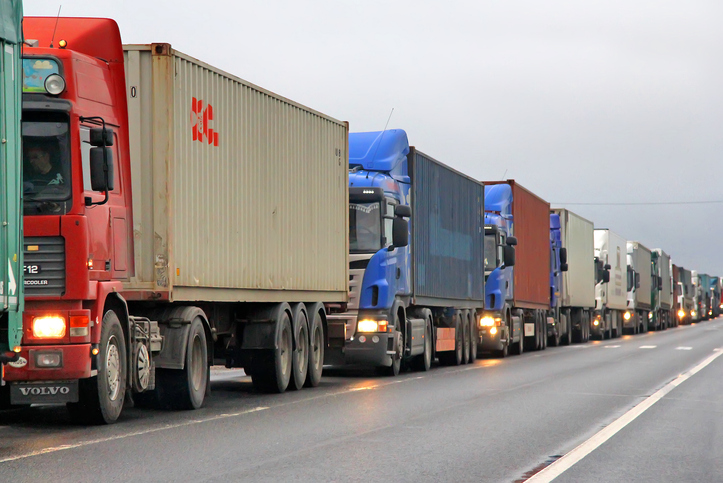
[S1] https://www.britishchambers.org.uk/news/2024/02/scale-of-red-sea-disruption-revealed/
[S3] https://www.usni.org/magazines/proceedings/2021/may/suez-canal-and-global-trade-routes